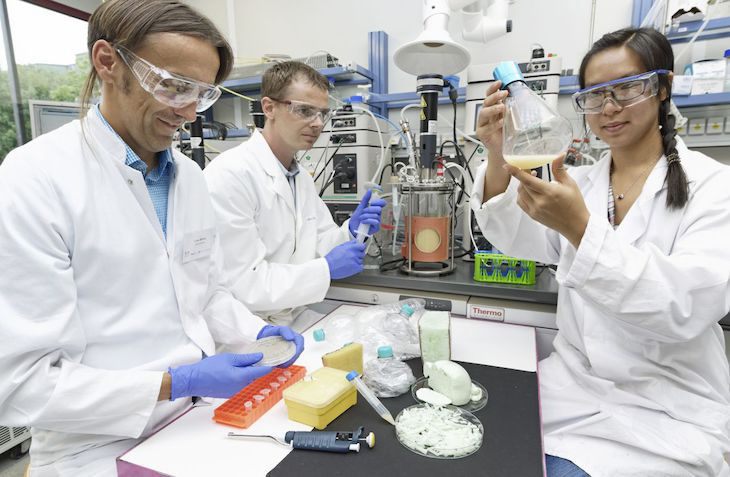
Germany alone faces millions of tons of plastic waste annually; most of this waste is incinerated. An innovative project is currently running at RWTH under the coordination of the Aachen biologists: microbes are coaxed to transform components of crude oil-based plastics into bioplastic.
It is the first RWTH-coordinated collaborative project under Horizon 2020, the EU’s framework program for research and innovation. The funds for the project were acquired by Professor Lars Blank and Dr. Nick Wierckx from the Chair of Applied Microbiology at RWTH Aachen. In P4SB, the abbreviation for From Plastic waste to Plastic value using Pseudomonas putida Synthetic Biology, the University is working with ten other partners from Germany, Ireland, Spain, France, and Great Britain to develop a new recycling cycle for plastic waste.
Problematic Plastic Waste
“The EU has strict standards for recycling plastic waste,” explains Blank. “By 2020, 50 percent of PET plastic, which is used in beverage bottles for exampe, should be recycled. Currently 30 percent is recycled. And polyurethane or PU foams, which are used in mattresses, car seats, or as insulating material, are to be 70 percent recycled. Under five percent is currently recycled.” Most of this type of waste ends up in incinerators even though it is reusable material – albeit a problematic one. Some plastics need around 500 years before they full decompose. In countries that don’t have a recycling infrastructure plastic waste lands in the countryside or sea, where it becomes the source of a lot of damage.
Plastic-Eating Organisms
The EU’s strict recycling quotas can be met in the long-term if researchers manage to turn bacteria into plastic-eating organisms. The evaluators, who reviewed the project proposal in the beginning, gave the go ahead. “We are facing great challenges, because some processes have only been known till now in individual steps, some only in theory even,” emphasized Blank. In the consortium experts will contribute their expertise from the fields of synthetic biology, metabolic engineering, enzymology, chemical engineering, polymer science, and environmental research.
The group of researchers is planning the following steps: First they will add enzymes to plastic waste that has been reduced to small pieces so that the enzymes can break apart the polymer bonds into monomers and individual building blocks. In the second step the bacteria eat the monomers to transform them into bioplastic, during which they incorporate certain characteristics. Finally, the bacteria excrete bioplastic building blocks.
Joining the Individual Steps
The last step is currently still theoretical: If the principal is successful in the lab, the bacteria would not have to “die” after the third step as they have been, so that the researchers could access the bioplastic. Rather, these tiny organisms could survive and consistently repeat steps two and three. Blank: “It’s not just important to implement the individual steps. We have to join them together and develop the tools do so.” The whole process is expected to work on the laboratory scale in four years. It will take an ordinate amount of time however, to develop the process on an industrial scale, where the bacteria eat plastic waste by the ton and transform it into bioplastic. The RWTH researchers are confident though that they will come closer to finding a solution in the next few years.
Contact
Lars Blank
phone: +49 241 80 26600
email: Lars.Blank@rwth-aachen.de
Source
RWTH Aachen, press release, 2016-03-16.
Supplier
European Union
Horizon 2020
Rheinisch-Westfälische Technische Hochschule Aachen (RWTH)
Share
Renewable Carbon News – Daily Newsletter
Subscribe to our daily email newsletter – the world's leading newsletter on renewable materials and chemicals